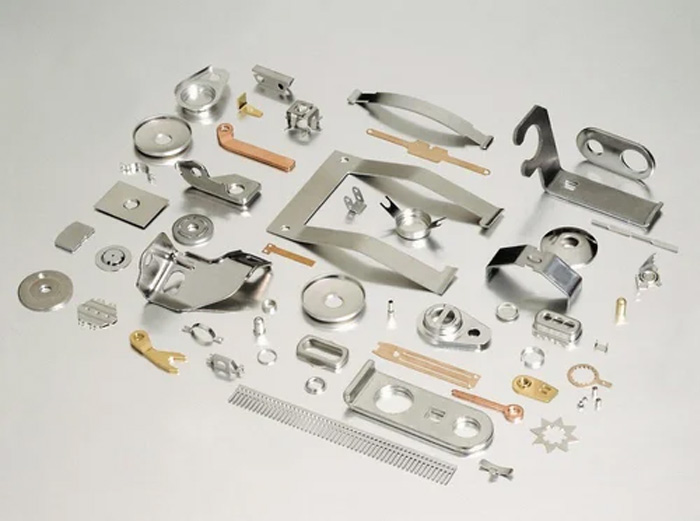
Ambani Metals is a leading name in the industry, specializing in high-volume, precision metal stamping manufacturing. With a commitment to excellence, Ambani Metals excels in producing precision sheet metal stamping parts that meet the most demanding standards across various industries. Utilizing advanced technology and expert craftsmanship, Ambani Metals delivers precision metal stamping solutions that ensure accuracy, consistency, and durability. Their expertise in manufacturing precision sheet metal stamping parts makes them a trusted partner for clients seeking reliable and high-quality components tailored to their specific needs.
These precision sheet metal stamping parts are used in cars, aeroplanes, industrial engineering, electrical and electronics, defence systems etc. Ambani Metals is equipped with the latest machinery, manufacturing unit, technology and an experienced team of precision sheet metal stamping professionals to offer good results.
Types of Precision Metal Stamping Products
What is Metal Stamping?
Precision metal stamping is a high-precision manufacturing process used to produce complex and intricate metal parts with exceptional accuracy and repeatability. This technique involves using a die and press machinery to shape flat metal sheets into specific precision metal stamping parts that meet tight tolerances. Precision metal stamping is essential in various industries, including automotive, electronics, medical, and aerospace, due to its ability to create components with consistent quality and minimal waste. The versatility of precision metal stamping allows for the production of a wide range of precision sheet metal stamping parts, from small connectors and clips to intricate brackets and enclosures, making it a critical process for industries requiring high-quality metal components.
Benefits of Metal Stamping & Pressing
- Cost Effective- Flexibility is unquestionably what makes metal stamping highly popular in various industries. It allows for metal to be shaped in tiny sizes and complex forms as per the requirement. During the process of pressing, however, specifications can be adhered to without any trouble. Metal stamping is cost-effective when sheet metal parts are manufactured in high volumes and large quantities. Metal pressing is the right solution to produce precision machine parts in bulk at a low cost of production.
- High Quality - Metal stamping is a method known for the manufacturing of high-quality machine components. Sheet metal stamped parts have proven to be so reliable that they have been used in complex operations also in various industries. Flexibility is unquestionably what makes metal stamping highly popular in numerous industries.
- Remarkable Accuracy - Probably the greatest advantage of metal stamping is the level of precision, which reaches a micron level. The sophistication and detailed nature of this process enables manufacturers to shape metal in the most complex forms with the help of innovative technology. The possibility for error is virtually minimal because of the use of sensors and camera systems, which inspect the dimension in the course of the process.
We can manufacture precision metal parts and components with a capacity from 5 tons to 300 tons in our in-house state-of-the-art production facility. We use high-quality metals including Stainless Steel, Brass, Copper, Alloy Steel and Aluminium to produce precision metal parts.
Different Precision Metal Stamping Methods
Normally, stamping refers to a single operation where a portion of a part is formed in one machine before being moved onto another machine or set of machines. The process requires multiple dies on several pieces of equipment. Finishing and shaping are separate operations performed after the part has been through the various machines. Progressive stamping removes the need for multiple machines performing several functions and handling the workpiece in a single set of operations. A strip of rolled metal unrolls into a single die press with several stations that perform individual functions. Each station adds to what has been done previously resulting in a completed, finished part.
Progressive stamping simplifies the production of complex and intricate parts decreasing production time while increasing efficiency. Movements must be precisely aligned since the part is still connected to the metal roll. The first station separates the fabricated part from the rest of the metal. Progressive die stamping is ideal for long runs since the dies last longer and do not sustain any damage as a result of the process. As with several stamping processes, progressive stamping is repeatable. Each station performs a different cut, bend, or punch to gradually achieve the desired end shape and design. Progressive die casting is faster and has limited waste scrap.
Deep draw is a highly specialized process in metal stamping requiring properly equipped press equipment and engineering expertise. We have built a reputation in the industry as deep draw experts for manufacturing deep draw stamping parts. The deep drawing process is a forming process which occurs under a combination of tensile and compressive conditions. A flat sheet metal blank is formed into a hollow body open on one side or a hollow body is formed into a hollow body with a smaller cross-section.
Transfer die stamping uses a mechanical transport system to move the part from station to station. It is used for tube applications, frames, shells, and structural components. A die can be a simple single die or part of several dies lined up in a row. To perform transfer die stamping, the part is removed from the metal strip as it transfers between stamping stations. Transfer die stamping was developed to produce large parts and workpieces with the additional benefit of lower tooling costs.
Four slide, multislide, or four way stamping shapes the workpiece horizontally sliding it between four different tools. As the workpiece feeds, it is bent by each tool using a smooth set of processes. Each slide is driven by a shaft controlled by the rotations of a cam. The shafts are connected by a bevel gear with one electrical motor to power the shafts. The workpiece may be shaped with all tools working at once or in succession. The key to four slide stamping is the shafts, which allows the work piece to be shaped on all four sides.
Fine blanking is a special type of stamping that produces flatness and a sheared edge that is impossible with traditional stamping. Any secondary machining of parts is not required since profiles, web sections, and holes are completed in one process. To achieve the perfection of fine blanking, the blank is compressed between the upper and lower punches allowing the process to hold a very tight tolerance. The process is known for its high accuracy and smooth edges. It is done with hydraulic or mechanical presses or a combination of the two.
The three individual movements of the press are used to complete blanking - clamping, blanking, and ejection. Fine blanking presses operate at higher pressures requiring tools capable of withstanding those conditions. The total process is completed in a single cold stamping step.
Choosing Metals for Metal Stamping
Though there are thousands of metals that can be stamped, there are two general categories - ferrous and nonferrous where ferrous metals have iron and nonferrous do not. Nonferrous metals that are commonly stamped are aluminium, brass, bronze, gold, silver, tin, and copper. One of the factors that determine the formability of a metal is its carbon content, though carbon is only one of many factors.
Alloys, a compound of two or more metals, are commonly used in metal stamping. Each alloyed metal has special characteristics that have to be considered when being used for metal stamping. For example, non-standard alloys, such as beryllium nickel and beryllium copper, are excellent for metal working, forming, and shaping musical instruments and bullets.
A wide range of raw materials used for the sheet metal part stamping process :
- Stainless Steel
- Cold Rolled Steel
- Hot Rolled Steel
- Aluminium
- Brass
- Beryllium Copper
- Titanium
Various manufacturing methods on sheet metals can be classified as follows:
- Cutting and Shearing- Here the sheets are cut by using various tools. Blanking, piercing, perforation, notching etc. are various types of shearing operations.
- Bending Operation- The sheet metals are straining around a straight axis.
- Forming- Flanging and tube forming are forming operations to give shape.
- Drawing Operations- Cupping, drawing, and deep drawing are all drawing operations in which sheet metals are given cup or shell-type shapes.
- Reducing Operations- Necking type of operations.
- Squeezing- For example coining operation is done in closed dies applying large force.