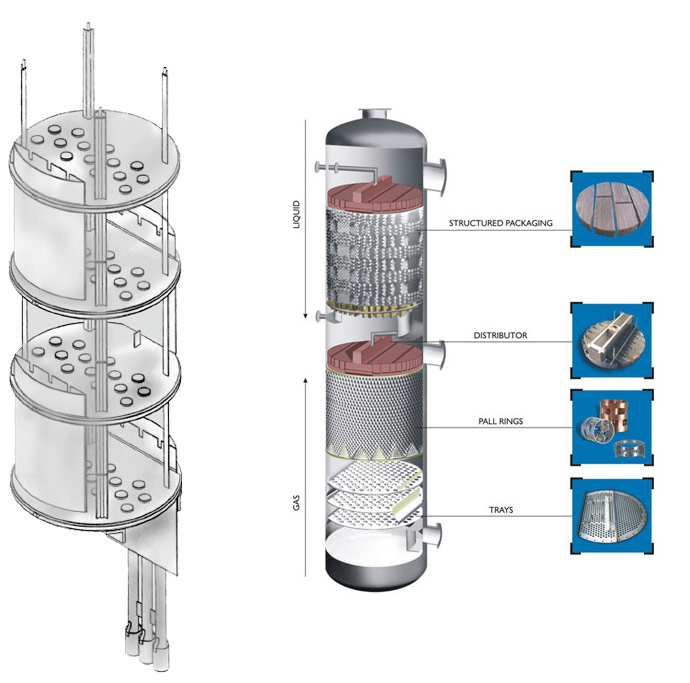
Fractionating Distillation Column
A fractionating distillation column, often referred to simply as a distillation column, plays a vital role in separating liquid mixtures based on their varying boiling points. As a leading manufacturer and supplier, Ambani Metals offers top-quality fractionating distillation columns, designed to meet the demanding needs of industries such as petrochemical, pharmaceutical, and beverage production.
How Fractionating Distillation Columns Work
The primary function of a fractionating distillation column is to separate a mixture of liquids into its individual components by leveraging the differences in their boiling points. These columns, supplied by Ambani Metals, consist of several trays or packing material stacked vertically, which create multiple stages for vapor-liquid contact, optimizing the separation process. Ambani Metals, as a reputable manufacturer and supplier, ensures that each column is engineered with precision to perform effectively in various industrial applications.
Process of fractionating distillation column
- Feed Introduction: The mixture to be separated, known as the feed, is introduced into the distillation column, usually at the top or bottom, depending on the type of column and the specific process requirements.
- Vaporization: Heat is applied to the feed mixture, causing it to vaporize. This is typically achieved by either direct heating or indirect heating through reboilers located at the bottom of the column. The vaporized mixture rises through the column.
- Contact with Stages or Packing Material: Inside the fractionating distillation column, there are several stages or trays (or packing material) stacked vertically. These stages are designed to provide maximum contact between the rising vapor and the descending liquid. The purpose of this contact is to facilitate the transfer of mass and heat between the vapor and liquid phases.
- Fractionation: As the vapor ascends the column, it comes into contact with the liquid descending from the upper stages. During this contact, components with lower boiling points tend to vaporize more readily, while components with higher boiling points remain in liquid form. This leads to the separation of the mixture into its constituent components based on their boiling points.
- Condensation: As the vapor rises, it reaches cooler temperatures towards the top of the column. This causes the vapor to condense back into liquid form. The condensed liquid, now enriched in the more volatile components, is collected at the top of the column.
- Reflux: To enhance separation efficiency, a portion of the condensed liquid (known as reflux) is often returned to the top of the column and reintroduced into the vapor stream. This reflux helps to increase the concentration gradient between the vapor and liquid phases, thereby improving separation.
- Product Collection: The separated components are collected at different points along the column based on their boiling points. The product with the lowest boiling point is typically collected at the top of the column, while the product with the highest boiling point is collected at the bottom. Intermediate products are collected at intermediate stages.
- Control Parameters: The functioning of the distillation column is controlled by various parameters such as temperature, pressure, reflux ratio, and flow rates. These parameters are adjusted to optimize the separation process and achieve the desired product purity and yield.
Type of distillation columns
Fractional Distillation Column
This is the most common type of distillation column used for separating a mixture of liquids with different boiling points. It consists of multiple trays or packing material to facilitate the separation of components based on their boiling points.
Packed Distillation Column
In a packed distillation column, the internal surface area is filled with packing material (such as structured or random packing) to enhance vapor-liquid contact and promote efficient separation. Packed columns are often used for processes requiring high capacity and efficiency.
Tray Distillation Column
Tray columns contain a series of perforated trays stacked vertically inside the column. Each tray serves as a stage for vapor-liquid contact, allowing for efficient separation of components. Tray columns are versatile and can handle a wide range of separation tasks.
Benefits of Fractionating Distillation Column
- Fractionating columns offer efficient separation of mixtures based on differing boiling points.
- They are adaptable to various industries and separation requirements.
- Fractionating Distillation columns can be designed in different sizes to accommodate different production capacities.
- Optimized designs reduce energy consumption during the separation process.
- Fractionating Distillation columns enable continuous production without interruptions.
- They effectively separate azeotropic mixtures, enhancing product purity.
- Fractionating Distillation columns integrate well with other unit operations for streamlined processes.
- They produce high-purity products meeting stringent quality standards.
Packing Material for Fractionating Distillation Column :
Packing materials play a crucial role in the functioning of a fractionating distillation column by providing surfaces for intimate contact between the vapor and liquid phases, thereby facilitating efficient mass transfer. There are several types of packing materials used in fractionating columns, each offering different characteristics suited for specific applications. Some common packing materials include:
- Structured Packing: Structured packing consists of specifically designed geometric shapes such as corrugated sheets or wire gauze arranged in a structured configuration. This type of packing offers high surface area for contact between the phases, resulting in improved efficiency and capacity compared to random packing.
- Random Packing: Random packing materials include various shapes such as spheres, rings, saddles, and cylinders. These packing materials are randomly stacked inside the column, providing a large interfacial area for vapor-liquid contact. Common materials for random packing include ceramic, metal, plastic, and glass.
- Structured Grid Packing: Structured grid packing consists of a series of vertical and horizontal grids arranged in a staggered pattern. This type of packing offers high mechanical strength and excellent liquid distribution, making it suitable for applications with high liquid loads and fouling tendencies.
- Intalox Packing: Intalox packing includes various configurations such as saddles, rings, and cylinders with internal or external fins. These packing materials are designed to provide enhanced liquid distribution and reduced pressure drop compared to traditional random packing
The selection of packing material depends on factors such as the specific separation requirements, flow rates, pressure drop limitations, corrosion resistance, and fouling tendencies. Engineers and designers carefully consider these factors to choose the most suitable packing material for each distillation application, ensuring optimal performance and efficiency of the distillation column.
Global Export of Distillation Columns | High-Efficiency Mass Transfer Solutions
Distillation columns are at the heart of separation processes in chemical, petrochemical, pharmaceutical, oil & gas, and food industries. With rising global demand for high-performance and energy-efficient separation technologies, the export of distillation columns has become a critical focus area for process equipment manufacturers worldwide.
Why Global Industries Rely on Distillation Columns
Distillation columns play a vital role in refining crude oil, purifying chemicals, producing high-purity solvents, and even separating gases in air separation units. They offer unmatched efficiency and scalability, making them essential in both large-scale industrial plants and specialty processing facilities.
Whether it's a fractionating column for petrochemical refineries, a reactive distillation unit for specialty chemicals, or a packed column for solvent recovery, global industries require customized column solutions that are durable, precise, and compliant with international safety and quality standards.
Our Expertise in Distillation Column Exports
We specialize in the design, manufacture, and global export of:
- Tray Columns : Bubble cap, Fixed Valve Tray and Sieve Trays
- Packed Columns : Structured and random packing systems
- Multi-product Separation Columns
- Fractionating & Rectification Columns
- Pilot & Laboratory Distillation Units
Our columns are engineered for optimized vapor-liquid contact, pressure drop control, and thermal efficiency. Each unit is manufactured with premium-grade stainless steel, alloys, or customer-specified materials and tested to meet ASME, ISO, and client-specific standards.
Export Markets
Ambani Metals, a leading manufacturer and global supplier of high-performance mass transfer equipment, such as distillation columns, column trays, structured packing, random packing, and internals, serves industries worldwide with precision-engineered solutions. Backed by advanced manufacturing expertise and strict quality control, Ambani Metals is well-equipped to export to a wide range of countries including those in the Middle East (Bahrain, Egypt, Israel, Jordan, Kuwait, Lebanon, Oman, Qatar, Saudi Arabia, UAE), Africa (Morocco, Tunisia, Ghana, Nigeria, Senegal, Kenya, Mauritius, Rwanda, Tanzania, Uganda, Zambia, Botswana, Eswatini, Lesotho, Namibia, South Africa), Europe (Germany, United Kingdom, France, Italy, Netherlands, Spain, Belgium, Poland, Czech Republic, Sweden, Denmark, Finland, Portugal, Hungary, Slovakia, Slovenia, Romania, Austria), Asia (Japan, South Korea, Singapore, Malaysia, Vietnam, Indonesia, Thailand, Philippines, Bangladesh, Sri Lanka, Nepal), and Pan-Pacific regions (USA, Canada, Mexico, Brazil, Chile, Colombia, Peru, Panama, Australia, New Zealand). With a strong global supply chain and a commitment to excellence, Ambani Metals continues to support critical processing industries across chemical, petrochemical, pharmaceutical, and refining sectors.
Partner with Ambani Metals - A Trusted Distillation Column Exporter
If you're seeking a reliable global supplier of industrial distillation columns, we are ready to serve your needs with precision, performance, and global compliance.
Contact us today to learn more about our distillation column range or to request a customized export quote.
FAQs
A fractionating distillation column is a vertical vessel used to separate mixtures of liquids based on differences in their boiling points.
Distillation columns operate by heating a mixture to vaporize its components, then condensing and collecting the vapors based on their differing boiling points as they rise through the column.
The main components include trays (or packing material), reboilers (for vaporization), condensers (for condensation), and reflux drums (for controlling reflux).
Types include fractional, packed, tray, reactive, azeotropic, extractive, and vacuum distillation columns, each suited to specific separation needs.
Distillation columns are used in industries such as petrochemicals, pharmaceuticals, food and beverage, and chemical processing for separating mixtures into pure components.