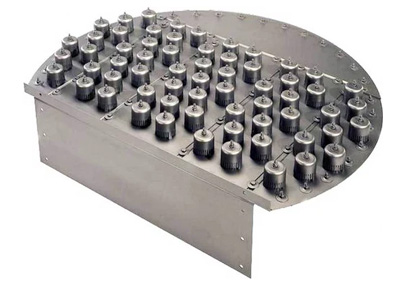
Bubble Cap Tray (AMB TRAY 1)
Bubble Cap Trays stand as the initial type of trays utilized in distillation procedures. Termed as "liquid sealed" trays, these trays incorporate vapor ascending through brief pipes called risers, each capped with a serrated edge or slots. Irrespective of the vapor flow rates, these trays sustain a steady liquid level, providing the benefit of accommodating a wide range of liquid flow rates.
A bubble cap tray has riser fitted over each hole, and a cap that covers the riser. The cap is mounted so that there is a space between riser and cap to allow the passage of vapour. Rising vapor passes through a series of bubble caps and is forced downward by the cap, finally discharging through slots in the cap, and finally bubbling through the liquid on the tray. Bubble cap trays are generally used when minimal leakage is allowed.
In bubble cap trays, vapor rising up through the tower / chimney reach the liquid by passing through bubble caps. Each bubble cap assembly comprises of a riser and a cap. The vapor rising through the column passes through the riser in the tray floor and directed downward by the cap, discharging through the slots in the cap and finally bubbling through the liquid on the tray. Bubble cap trays can't weep because of their design.
The main application of bubble cap trays, lies in their utilization within distillation columns for refining and separating liquid mixtures. Ambani's bubble cap trays are designed to optimize distillation processes in industries such as petroleum refining, petrochemical production, and chemical processing. These trays provide efficient mass transfer and separation of components, ensuring high purity and quality of the separated products. They are particularly suited for applications where precise separation is paramount, such as in the production of fuels, chemicals, and pharmaceuticals. Ambani's bubble cap trays are engineered to meet the rigorous demands of industrial distillation operations, offering reliability, durability, and performance to enhance overall process efficiency and productivity.
Features :
- Wide range of turn down ratios without weeping.
- Uniform Vapour Distribution Enhanced Mass Transfer
- Dimensional accuracy
- Precise design
- Improved efficiency characteristics
Material of Construction :
- SS 304/L, SS 316/L, 904L, 254SMO, Duplex, Super Duplex, Titanium, Hastelloy, Monel, Inconel, Copper or any metal/alloy as per customer request
Key Characteristics :
- Bubble Cap Tray used for low liquid loads. Very wide turndown ratio
Available Size :
- Bubble Cap Trays are available up to upto 6m with 50 - 100 mm caps
Bubble Cap Trays FAQs
A bubble cap tray is a component used in distillation columns for separating liquid mixtures based on their boiling points. It consists of a perforated tray with bubble caps evenly spaced across its surface.
Bubble cap trays work by promoting the interaction between rising vapor and liquid on the tray. The vapor bubbles through the liquid, creating a large surface area for contact. This promotes condensation of volatile components in the vapor, leading to separation based on boiling points.
Bubble cap trays provide efficient separation, uniform vapor distribution, and enhanced mass transfer. They are versatile, durable, and relatively easy to maintain.
Bubble cap trays are used in various industries including petroleum refining, chemical manufacturing, petrochemical production, natural gas processing, alcohol production, food and beverage industry, environmental remediation, and laboratory research.
Yes, bubble cap trays can often be retrofitted into existing columns to improve separation efficiency or replace worn-out trays. However, it's essential to consider factors such as compatibility with existing equipment and column design.
Yes, there are various tray designs such as sieve trays, valve trays, and structured packing that can also be used for distillation. The choice depends on specific application requirements and preferences.
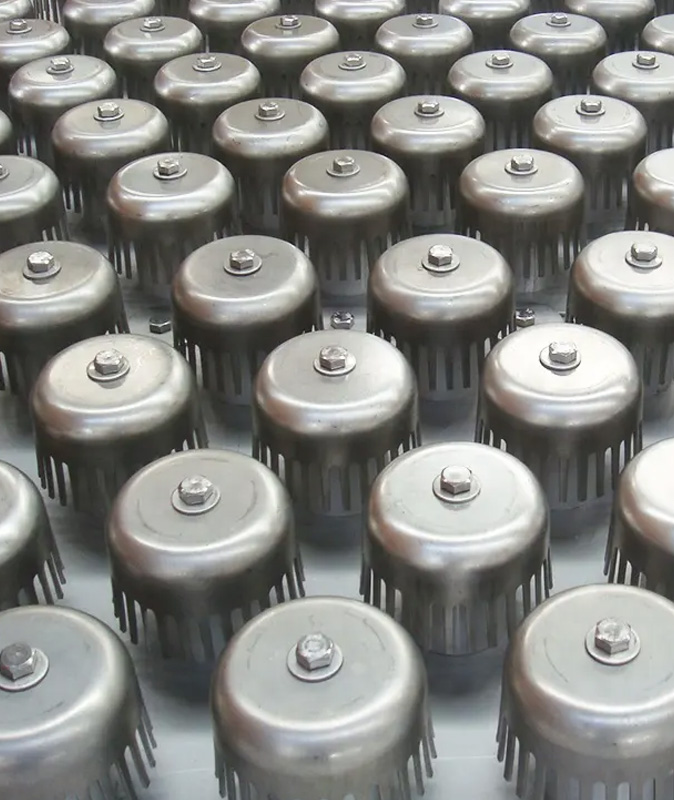
Bubble Cap (AMB TRAY 1)
Bubble caps are metal cup with notches or slots around the edge that is inverted over a hole in a plate in a bubble tower for effecting contact of vapors rising from the plate below and liquid already on the plate. Bubble caps are designed with a series of risers topped with slotted caps.
Bubble Caps are one of the devices in large-diameter fractional distillation columns that are designed to produce a bubbling action to exchange the vapor bubbles flowing up the column.
Ambani Metals offers bubble caps, bubble cap trays. Bubble caps consist of risers for vapor on the deck that are covered by caps. These caps are essentially inverted cups with slots around the perimeter that allow for mixing of vapor from the riser into the liquid on the tray deck. The riser cap assembly prevents weeping even at very low flow rates. This permits bubble cap trays to operate over a wide range of conditions, including very low turndown rates. Caps are available in many sizes and designs.
Bubble caps are used in following Industries :
- Chemical industry
- Pharmaceutical Industry
- Petrochemical Industry
Features of Bubble Cap:
Bubble caps are essential components in distillation columns, facilitating the separation of liquid mixtures based on their boiling points. These key features collectively contribute to the efficient operation of bubble caps in distillation columns, enabling the separation of liquid mixtures with high precision and throughput. Here are the key features of bubble caps:
Cap Shape
Bubble caps typically have a cylindrical or dome-shaped design. This shape helps to contain rising vapor and facilitates its distribution across the tray surface.
Perforations
The tray beneath the bubble cap is perforated with small holes or slots. These perforations allow vapor to pass through while retaining liquid on the tray.
Downcomer Area
Beneath each bubble cap, there is a downcomer area. This area allows liquid to flow from the tray above to the tray below, ensuring continuous liquid circulation within the column.
Bubble Cap Opening
Each bubble cap has an opening through which vapor can pass. This opening is typically smaller than the diameter of the cap, creating a bubble of vapor that promotes efficient contact between the vapor and liquid phases.
Bubble Cap Clearance
The clearance between the bottom of the bubble cap and the tray surface is carefully designed to optimize vapor-liquid contact. It ensures that the vapor passes through the liquid, creating bubbles that enhance mass transfer.
Materials
Bubble caps are commonly made from materials such as stainless steel or other corrosion-resistant alloys to withstand the harsh conditions inside the distillation column.
Spacing
The spacing between bubble caps on the tray is important for maintaining uniform vapor distribution and liquid flow across the tray surface. Proper spacing ensures efficient utilization of the tray area.
Sealing
Effective sealing between the bubble caps and the tray surface is crucial to prevent bypassing of vapor or liquid. Proper sealing ensures that vapor is forced to pass through the liquid on the tray, promoting effective separation.
Mechanical Stability
Bubble caps are designed to withstand the mechanical stresses and vibrations encountered during operation. This stability ensures the integrity of the tray structure over time.
Maintenance
Bubble caps should be designed for easy access and maintenance. This facilitates inspection, cleaning, and replacement as needed, minimizing downtime and maximizing the efficiency of the distillation process.
Choosing Ambani Metals as your bubble cap manufacturer offers several advantages :
- Reputation and Experience : Ambani Metals is a reputable bubble cap manufacturer with a solid reputation and a proven track record in manufacturing top-quality bubble caps that are robust, corrosion-resistant, with enduring performance.
- Product Quality and Standards : Select Ambani Metals as your bubble cap manufacturer, guaranteeing the production of high-quality bubble caps that comply with industry standards and regulations for materials, construction, and performance.
- Customization Options : Ambani Metals offers customization options to tailor bubble caps to your specific application requirements. This may include adjustments in materials, dimensions, cap configurations, and hole patterns.
- Technical Expertise : Ambani Metals specializes in manufacturing premium bubble caps with comprehensive support services. We have skilled engineers capable of recommending the ideal bubble caps for your distillation process and providing technical assistance throughout the project's duration.
- Production Capacity and Lead Times : Ambani Metals operates its own manufacturing facility, ensuring production capacity and turnaround times that align with your demand and project schedules. We have the flexibility to adjust our production capacity as necessary to accommodate urgent orders.
- After-Sales Support and Warranty : Ambani Metals offers after-sales support for bubble caps manufactured by us. Our team of experienced engineers is available to address any concerns you may have regarding bubble caps.
Bubble Caps FAQs
Bubble caps are essential components utilized in distillation columns for separating liquid mixtures based on their boiling points. They are designed to promote the interaction between rising vapor and liquid within the column. Structurally, bubble caps resemble inverted cups, featuring slots or holes on the top surface. These caps are evenly distributed across the tray within the column. As vapor ascends through the liquid on the tray, it passes through the bubble caps, generating bubbles. These bubbles aid in distributing the vapor uniformly across the tray, enhancing contact between the vapor and liquid phases. Consequently, this facilitates efficient separation of components, as more volatile substances condense and are collected based on their differing volatilities. Overall, bubble caps play a crucial role in ensuring efficient mass transfer and separation within distillation processes across various industries.
Fixed Bubble Caps
These are the most basic type of bubble caps. They are permanently fixed onto the tray surface and do not move during operation. Fixed bubble caps are simple in design and offer reliable vapor distribution.
Movable Bubble Caps
Movable bubble caps are designed to move vertically within the tray. They can lift or lower in response to changes in vapor flow rates, ensuring more uniform vapor distribution and better control over the distillation process.
Sieve Bubble Caps
Sieve bubble caps feature a perforated plate with holes or slots instead of a solid surface. They allow vapor to pass through the holes while retaining the liquid on the tray. Sieve caps are effective at promoting vapor-liquid contact and are commonly used in high-capacity distillation columns.
Dual-Flow Bubble Caps
Dual-flow bubble caps are designed to facilitate the passage of both vapor and liquid through the tray. They feature additional channels or passages that allow liquid to flow underneath the bubble cap while vapor bubbles through the top, enhancing mass transfer efficiency.
Multi-Orifice Bubble Caps
Multi-orifice bubble caps have multiple holes or slots on the top surface, allowing for increased vapor flow rates and improved vapor distribution. They are often used in large-diameter distillation columns where high vapor velocities are required.
Application of bubble caps in fractional distillation is to enhance vapor-liquid contact, ensuring uniform vapor distribution and controlled bubble formation. This facilitates efficient separation of components based on their differing volatilities, leading to the production of purer fractions.
Ambani Metal utilizes metal fabrication techniques such as stamping, machining, or welding to create the desired shape and perforations in the bubble caps, ensuring uniform vapor distribution and efficient separation of components in distillation processes. Ambani Metal adheres to industry standards and quality control measures to ensure the reliability and performance of the bubble caps.